智能AGV 在冲压车间的应用
文/赵博,孙刚,吴明华,张秀花·一汽-大众汽车有限公司
随着汽车市场的飞速发展,智能化物流设备成为工业未来的发展方向。对于冲压车间,传统的冲压工艺是冲压线末尾生产出零件后,人工装箱,再通过叉车运输,将冲压零件料箱运输到库房。一汽-大众冲压车间于2017 年首次采用了冲压AGV 工艺,替代了叉车运输,提升了冲压智能化物流能力,本文介绍了智能AGV 系统及其在冲压车间的应用。
智能AGV 系统的应用对冲压车间来说是一次全新的技术变革。通过智能AGV 的应用,冲压车间可以避免叉车进入生产区域,对车间安全、自动化率提升、能源节省等多方面都有很大帮助,同时,也为企业下一步实现智能仓储体系打下基础。下面就从智能AGV 的结构、不同AGV间的区别等方面详细介绍一下智能AGV 在冲压车间的应用。
智能AGV 结构
如图1 所示,AGV 系统构架可以分为中央控制单元、壳体、升降销、动力单元、操作面板、安全防护、安全检测、传感器8 个部分。通过磁导航传感器,可以检测到地面磁条位置,从而通过相对位置,经过中央控制单元计算,控制舵轮,调整AGV 运行姿态。通过RFID 地标传感器,可以得到当前的绝对位置,并且根据绝对位置,通过无线网络,得到来自控制系统的任务指令,进行物流运输,AGV 实物如图2 所示。
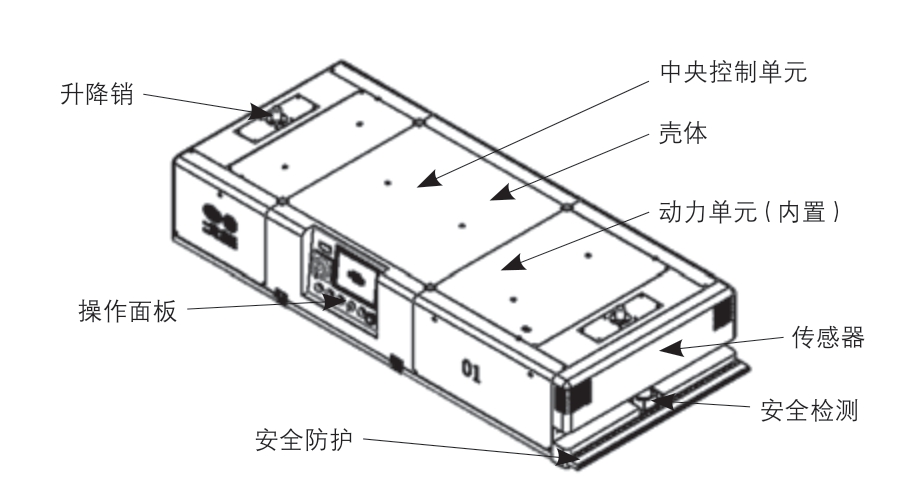
图1 智能AGV 结构图
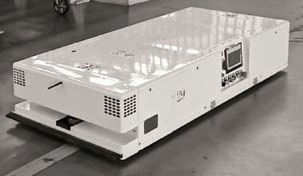
图2 智能AGV 实物
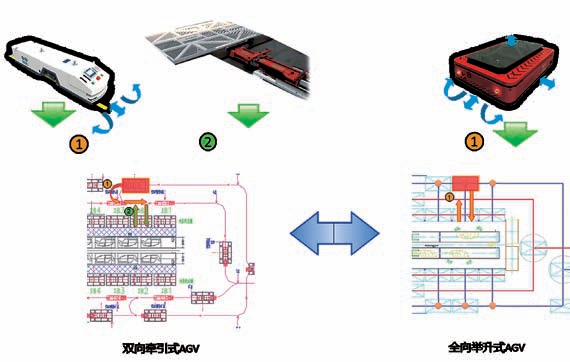
图3 AGV 的应用形式
冲压车间不同种类AGV 的区别
物流行业中应用的AGV 有很多种,按AGV 小车的导航方式可分为:电磁导航AGV 小车,磁条导航AGV小车,二维码导航AGV小车,激光导航AGV小车,惯性导航AGV 小车,视觉导航AGV 小车。按AGV小车移载方式(执行机构或用途)又可分为:叉车式AGV 小车,牵引式AGV 小车,背负式AGV 小车,滚筒式AGV 小车,举升式AGV 小车,装配式AGV小车。
根据AGV 结构不同,冲压车间采用的AGV 主要有三种类型:(1)潜伏双向牵引式AGV;(2)潜伏全向牵引式AGV;(3)全向举升背负式AGV。采用这三种类型AGV 的原因是由于冲压车间的料箱尺寸大小不一,而且重量也不相同,其他种类AGV 很难覆盖如此多品种的料箱。并且,冲压料箱数量非常多,如果要标准化冲压料箱,会导致库房面积与料箱成本的提高。而潜伏或背负式AGV,可以通过通用的托盘,在一定程度上减少AGV 对料箱标准化的要求,实现最大程度的通用。
由于第三种AGV 是在第二种AGV 上进行的更新,因此,本文着重介绍第一种和第三种AGV 在冲压车间应用的区别,如图3 所示。
双向牵引式AGV 是单舵轮AGV,具备前后及转弯运输的能力。由于冲压线尾空间要求,其运行需要与伸缩机构相配合。每次运行过程中,员工在压机线边呼叫AGV;AGV ①牵引着存放料箱的托盘运行至伸缩机构所在位置②处;AGV 与存放料箱的托盘分离,继续向前运行;伸缩机构夹住存放料箱的托盘,拉回压机线边,员工进行摆件。
全向举升式AGV 是双舵轮AGV,并且有举升电机,可以将料箱进行举升。通过双舵轮,全向AGV可以进行横移,所以路线规划更加简单。通过举升,可以减少压机线边固定机构。每个AGV 都是一个独立的运行单元,从而大大提升了AGV 系统的柔性,通过磁条路线的变更及系统程序的更改,就可以对生产线节拍变化等情况进行重新匹配。
AGV 安全系统
对比叉车物流,智能AGV 使冲压车间的物流安全得到了大幅度提升。AGV 的安全装置有。
(1)激光扫描仪。在AGV 小车行驶时,会在AGV 行驶前方形成一定的探测区域,AGV 根据与前方物体距离进行减速和停止动作,如图4 所示。
(2)报警灯及蜂鸣器。主要是通过光闪烁和声音来提醒车间的工作人员注意安全。
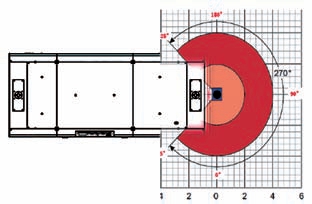
图4 AGV 传感器扫描区域
(3)机械防撞边缘。AGV 前方设置接触式机械防撞安全边缘,当安全边缘与障碍物发生碰撞,AGV会停车保护。
(4)紧急停止按钮。特殊情况需要紧急停止AGV,可通过紧急停止按钮实现。
AGV 监控调度系统
如图5 所示,监控调度系统通过无线网,实时监控AGV 运行状态与位置,同时也对自动机构、充电设备等进行监控,确保稳定运行。监控调度系统具备关键通道交叉路段实时交通管制能力,避免AGV 发生碰撞。系统可以与冲压MES 系统进行数据交互,进一步提升冲压车间数字化能力。
AGV 实际应用总结
通过冲压AGV 实际应用,经验总结如下。
(1)节拍与路线规划。
由于冲压车间生产不均衡,高峰值节拍可达到40s 下线一个料箱(冲压侧围零件生产),低谷值在300s 一个料箱(冲压内板零件生产),所以需要对程序及规划路线进行设定,系统需要判断零件的节拍,进行AGV 路线的调节,不同节拍采用不同路线、不同速度,从而优化AGV 的数量。通过不断的路线优化及调试优化,一汽-大众冲压车间仅用29 台AGV,就完成了2 条高速冲压线的物流转运。
(2)减振。
AGV 走轮为刚性走轮,在AGV 实际运行过程中会产生很大振动,所以AGV 结构设计中需要考虑采用弹簧减振,减小振动幅度,从而降低故障率。定位销每次在与托盘车挂靠的过程中,也会产生振动,需要采用缓冲机构,减轻定位销的冲击,同时,多定位销定位,可以提高定位销与托盘车的匹配性,减少匹配过程中的摆动,分担作用力。
(3)配重。
冲压车间地面一般为钢纤维耐磨地面,AGV 在牵引1 吨左右的冲压件在地面行车时,会出现打滑脱离磁条轨道的情况。需要在AGV 前后预留配重空间,进行配重调整。同时,需要选择大功率舵轮,避免后续由于配重调整导致动力不足。
(4)偏载。
由于AGV 搭载的托盘为通用托盘,因此一般按照最大尺寸进行设计,为了保证料箱与摆件人员距离最小,料箱会放置在通用托盘的一侧而非正中心,因此运行过程中会出现偏载的情况。需要通过合理布置脚轮、AGV 配重,程序补偿,来抵消偏载造成的行驶角度不正。
(5)转弯半径。
冲压线尾空间有限,为了保证不过多占用空间,一般要求双向牵引式AGV 转弯半径小于1.5m,因此需要在布置托盘脚轮过程中一定程度的向中心布置,减少转弯半径。
(6)舵轮及磁导航传感器布置。
舵轮作为整个AGV 的动力轮,位置十分关键,舵轮如果经过磁条路线区域,会对磁条造成破坏,因此要考虑磁导航传感器偏置,避免舵轮压过磁条路线。
(7)脱轨问题。
AGV 小车运行过程中,经常会出现脱轨问题。情况1:如果是单舵轮AGV 向前运行过程中脱轨,需要考虑舵轮布置过程中尽量靠前布置。情况2:如果是后退过程中脱轨,由于后退主要出现在冲压抽检、返修等工位,这时可考虑增加导向机构进行辅助导正。
(8)速度选择。
AGV 小车速度不是越快越好,行驶太快会增加刹车距离,同时,惯性可能导致货物倾倒,存在较大安全隐患。速度过大,还会导致转弯过程中脱轨,重复加减速,能耗也会增加。根据测试,冲压AGV 直线速度一般不大于1m/s,转弯速度不大于0.4m/s,此速度可以保证AGV 稳定运行。

图5 监控调度系统原理图
(9)运营维护。
前期项目规划时需要综合考虑AGV 生命周期的监管、维护和备件成本,例如:其动力电池一般3 ~5年需要进行更换。
结束语
智能AGV 的使用确实给冲压车间带来了很大益处。
首先,安全性得到了大大提高。冲压零件生产过程中,料箱的转运流量不是一成不变的,比如生产侧围零件时,压机线尾物流转运量非常大,侧围料箱长度尺寸大于3500mm,但转运空间却十分有限,叉车转运时,经常会出现磕碰等情况。采用AGV 后,避免了此种情况的发生,减少了器具的维护成本,同时也减少了可能导致的安全风险。其次,经过估算,采用AGV可节省约20%的能源消耗。此外,AGV的采用,还节约了物流运营成本。最后,智能AGV 系统可以与冲压MES 系统等进行数据交互,同时,为下一步实现智能化无人冲压仓储物流打下基础,提升了冲压车间数字化、智能化的能力。
赵博
冲压规划工程师,主要从事冲压车间规划、数字化工厂、新技术应用等工作,曾负责参与规划一汽-大众佛山、青岛、天津、长春生产基地,并主持完成天津8100t 高速冲压生产线安装等多个项目工作。
随着汽车市场的飞速发展,智能化物流设备成为工业未来的发展方向。对于冲压车间,传统的冲压工艺是冲压线末尾生产出零件后,人工装箱,再通过叉车运输,将冲压零件料箱运输到库房。一汽-大众冲压车间于2017 年首次采用了冲压AGV 工艺,替代了叉车运输,提升了冲压智能化物流能力,本文介绍了智能AGV 系统及其在冲压车间的应用。