一种解决包边面品质量缺陷的方法
文/张宇,秦海斌,马延峰·恒大新能源汽车集团天津公司
随着汽车工业的发展,包边总成质量的要求也随之提高,而现场包边操作时常会出现由于包边导致的面品质量缺陷问题。本文旨在通过改变滚边轨迹和滚轮角度的方式来解决机盖包边总成的面品成形质量缺陷,对提高包边总成和整车产品品质,有一定指导作用。
包边是车身制造中的一大重要工艺,提升包边品质对于提升产品的品质和整车光栅的光顺性有很重要的作用。在制造中减少包边后总成零件的质量缺陷,也能够有效降低现场调试的工作强度。
目前在包边领域主要存在4 种解决方案。
(1)包边模:借助压力机提供动力,完成40°~45°预包边和0°终包边,方案成熟,质量稳定,生产节拍快,批量高。但缺点是车型换代时,需要再次开发新的包边模具,柔性化生产效率低。
(2)机器人滚边:借助滚边夹具、滚轮系统、机器人和控制程序,根据具体零件造型通过3 ~5 轮次的滚轮滚压外板零件完成包边工作。滚边方案柔性化高,可以根据不同零件的实际生产情况,采用不同的机器人与胎模的灵活搭配,即实现一机多模或一模多机的生产方式。
(3)气动包边机:借助气缸提供动力,通过包边镶块压合外板零件完成包边。此方案调试周期长,动作也不符合钣金翻折的特点,故质量问题较多。
(4)手工包边:依赖于钳工的个人技能,包边一致性差,生产效率低。
综上,目前大多汽车厂采用滚边机器人作为包边工作的解决方案。本文以我司现场实际生产中的机盖总成为依据,尝试从模拟分析的角度,解决零件的质量缺陷。
实验背景
我司在一款车型的生产中,机盖包边总成一直存在质量缺陷,且久治不愈。现场问题如图1 所示,整个机盖包边总成,存在16 项质量问题,亟待解决。大体可分为以下3 类。
(1)1 ~9 号是机盖总成外凸侧在包边后的面品缺陷,表现为油石打磨后的油石断线。
(2)10 ~15 号是机盖总成风挡玻璃侧在包边后的面品缺陷,表现为油石打磨后的油石断线。
(3)16 号是机盖总成正面左棱线处的面品缺陷,表现为油石打磨后的油石断线。此问题由于是单件成形时发生而且经过滚边成形缺陷并无放大,故16 号问题不在本文解决方案之列。
创建Autoform 仿真实验模形
(1)创建工具体模形。

图1 实际生产问题
在3D 制图软件UG 中创建滚边所需工具体的几何数形,并导入仿真分析软件Autoform 中进行工具体的设置。胎模选取外板最外侧120mm 宽度为支撑面,并依据现场情况布置吸盘位置。采用现场实际生产用的“90°→45°→0°→水滴”,4 轮次的包边角度,设计不同角度下的包边滚轮,以上如图2 所示。
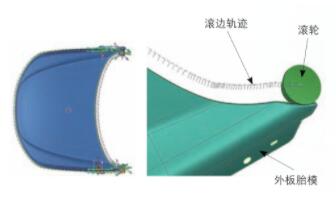
图2 包边工具体实验模形
(2)设置实验板料。
外板零件材质Superlite200(铝板),料厚0.9mm。内板零件材质Ecolite163st(铝板),料厚0.8mm。调整内外板单件数形的空间位置到车身坐标,以实际生产中单动拉延的运动方式,模拟计算冲压单件全工序成形过程,并输出可用于滚边分析的计算结果(.asm),以此模拟结果,作为板料数据导入Autoform计算。图3 为计算后的单件回弹数据,计算结果与现场调试情况一致,可用于本实验分析。

图3 冲压内外板单件计算结果
(3)创建滚边轨迹。
在滚边的初始位置布置滚轮,依据滚轮中心到零件边缘的距离,偏置外板零件最外侧圆角切线至滚轮中心,生成此滚轮的滚边轨迹。零件依照现场实际生产情况,需要设置3条滚边通道,每个通道需要翻4次,共计12 条滚边轨迹,如图2 左图所示。
(4)摩擦系数为0.15。
(5)滚轮速度为100mm/s。
(6)预包边的滚边压力设置为刚性。
滚轮依据设计好的滚边程序运动,内板零件布置于外板零件之上,外板零件的翻边面因受到滚轮的作用力而发生材料变形,并基于多轮次的滚边进而产生塑性变形,得到想要的总成零件形状。
包边模形仿真结果分析
通过以上设置计算后,得到一个分析结果,如图4 所示,通过计算结果和现场总成零件的质量检验结果的对比,计算结果可以比较全面且真实的反应现场情况,可以用于实验模拟分析。
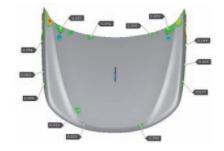
图4 滚边成形仿真模拟结果
当滚边发生在多料翻边一侧,即机盖外凸一侧,无论是滚边成形过程还是滚边结束状态,包边面上都出现了明显的波浪,为成形质量缺陷,如图5 所示。而本章节以下内容,将通过尝试更改滚边参数,来减轻这种质量缺陷。

图5 滚边成形过程状态
外凸侧机盖质量缺陷的解决
外凸一侧即图1 中1 ~9 号问题点区域。此区域在翻边和包边时都是多料翻边,易出现翻边起皱,在零件回弹上,经常呈现两边塌中间翘的现象。此经验现象正好与模拟结果能够对应,如图6 所示。
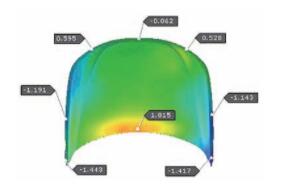
图6 总成零件回弹结果
初始状态的外板件,在机器人滚边的作用下,板料由外向里不断折叠,发生塑性变形,最终成为机盖总成的零件形状。在这过程中,外板零件在外凸一侧,由于翻边时材料由外向里的收缩流动,板料受压应力的作用,而且此处根据零件造型本就是翻边多料的一侧,板料流动更加不均匀,就会产生起皱缺陷,特别是在A 面曲率变化急剧的位置,由于轨迹不变而形面曲率不同导致的包边角度变化,滚轮的压应力的作用会急剧变化,也非常容易在立壁产生波纹。
由于此零件是周圈水滴包边,且单件翻边时两侧平均翻边角度是150°,机头侧平均翻边角度是130°,考虑到生产效率,最初车间采用的是“90°→45°→0°→水滴”的包边方案。
1 ~9 号的质量问题,是由于多料翻边产生了成形质量缺陷。首先,调整此处滚边轨迹从单轨迹改为双轨迹,如图7 所示。考虑到两侧一样形状的零件,滚边前后顺序不一样,滚轮对零件的压合导致成形应力不一致,为保证左右结果一致做此调整。

图7 滚边轨迹调整
其次,调整滚轮的角度从“70°→30°→0°→水滴”,调整到“80°→40°→0°→水滴”。目的为减缓滚边第一次折弯导致的多料在后续折弯时的累积,如图8 所示。
风挡侧机盖质量缺陷的解决
风挡一侧即图1 中10 ~15 号问题点区域。此区域在翻边和包边时都是少料翻边,易出现翻边开裂,在零件回弹上,经常呈现两边翘中间塌的现象。此现象也与模拟结果能够对应。
由于此处是水滴包边,且单件翻边时此处平均翻边角度是100°~120°,考虑到生产效率,最初车间采用的是“90°→45°→0°→水滴”的包边方案。而现在调整滚轮的角度从“90°→45°→0°→水滴”,到“70°→35°→0°→水滴”。目的是减缓第二、三轮次滚边时,零件折弯的少料趋势,让零件最后的折弯少料趋势逐渐减缓,如图9 所示。
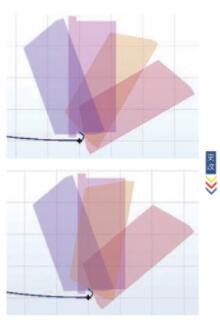
图8 滚轮工作角度调整

图9 滚轮工作角度调整
模拟结果评价
经过以上调整,如图10 所示,1 ~15 号的面品缺陷不同程度的得到了减缓,可以看出,改变滚边轨迹和滚边角度的方法可以有效减缓包边后的面品缺陷,滚边轨迹和滚轮角度则要通过零件造型和成形状态来确定,并需要经过模拟计算的验证。

图10 机盖总成面品质量变化
结束语
通过在滚边操作中,在零件对称侧设计对称的滚边轨迹,可以控制每一次板料折弯的趋势和应力分布相同,进而改变由于轨迹不一致而导致的零件左右不一致现象。
在多料翻边的一侧尽量减缓滚轮首次触料而导致的起皱,减缓起皱在后续折弯的堆积会改善滚边零件的质量;而在少料翻边的一侧尽量减缓后续滚边的少料程度,通过多次成形,减缓少料的趋势而导致的质量问题。
由于软件是冲压软件,而包边的工作在焊装完成,横跨了两个专业,故包边分析模块在焊装车间内并没有得到广泛的利用。而通过上面的例子可以看到,分析软件的设置在符合生产现场情况的条件下,可以得到较为真实的结果。本文通过此实例的说明,期望能达到抛砖引玉的效果,期望在未来包边的调试及同步工程上,都能有效的把模拟分析利用起来,尤其是在前期开发阶段,若能有效利用好分析软件,在前期改善零件自身造型带来的问题,可有效的减少现场的调试工作量。
随着汽车工业的发展,包边总成质量的要求也随之提高,而现场包边操作时常会出现由于包边导致的面品质量缺陷问题。本文旨在通过改变滚边轨迹和滚轮角度的方式来解决机盖包边总成的面品成形质量缺陷,对提高包边总成和整车产品品质,有一定指导作用。