汽车冲压件中滑移线问题的产生及解决方案
文/张宇,秦海斌,马延峰·恒大新能源汽车集团天津公司
滑移线是汽车外覆盖件在冲压生产中一种常见的表面缺陷,滑移线的出现严重影响了冲压件的表面质量和产品外观。本文主要对滑移线的产生原因和解决方案进行了详细的研究,为冲压设计和生产时避免滑移线的出现,提供了参考。
伴随时代的进步,大家对于车辆的审美标准也在不断提高,汽车的产品造型也在不断地变化。伴随汽车造型设计的演变,车辆外观有一个明显的变化趋势,就是越来越“见棱见角”。但是,这种造型大大增加了车身冲压件的生产难度。
在汽车业有这样一种分类法:A 面,车身外表面,白车身;B 面,不重要表面,比如内饰表面;C 面,不可见表面。这其实就是A 级曲面的基础。A 级曲面,必须满足相邻曲面间之间隙在0.005mm以下(有些汽车厂甚至要求到0.001mm),切率改变(Tangency Change)在0.16度以下,曲率改变(Curvature Change)在0.005 度以下,符合这样的标准才能确保外板件喷漆后在光照条件下不会出现严重的光反射问题,常见的汽车A 级曲面表面缺陷有压痕、塌陷、面畸变、冲击线以及滑移线等,其中滑移线是模具车间调试时最难解决的问题。
滑移线是冲压成形后金属板料在非接触面上的可见带状曲线,在冲压过程中,当板料流经模具圆角时经历弯曲、反弯曲和拉伸时会产生滑移线。本文主要从产生原因,解决方案两方面对滑移线进行研究,为实际冲压生产中解决滑移线问题提供指导。
滑移线定义
2015年12月,阳光佳苑一期一条主管线突然崩裂,无法正常供暖。为尽快恢复供暖,陈建华脱掉棉衣,只穿着单薄的工作服,第一个跳进脏水沟里更换主管线,刺骨冰冷的水冻得他瑟瑟发抖。经过几小时的抢修,才将管线安装完成。
通过图1 可以看到一个后背门外板的拉延工艺,冲压件在两条棱线处均有不同程度的滑移情况发生。主棱线A 沿箭头方向最大滑移4.2mm,副棱线B 沿箭头最大滑移2mm。由于板料在拉伸过程中,存在流动性,板料在接触棱线(图1 中黄色线处)发生材料局部硬化后,会继续流动,当流出圆角后,就会形成缺陷痕迹。

图1 滑移线
图2 展示的是侧围角窗处,生产现场实际的滑移线缺陷。这种滑移线缺陷(图示中现场漆笔标记的二重线位置)严重影响了汽车车身覆盖件的表面质量,极大增加了模具开发的工作周期及生产成本。因此,在冲压工艺设计阶段,必须对模具开发前的滑移线风险进行预测,以防止冲压生产中对模具和工艺进行大量的变更。
在车身上主要发生部位
通过图3 中的红色线条,可以看到滑移线频发的位置,主要集中于车身外表面的特征线上。如车辆的腰线、机盖的造型线、行李厢的弯折线、轮眉造型线、角窗灯口等。这些位置是体现车辆造型特征的地方,滑移线缺陷频发,给车身造型和观感造成极大减分,滑移线也成了必须要解决掉的问题。
滑移线产生原因
大多数滑移线发生于成形初期或成形中间,滑移线的生成过程分为4 个阶段。第1 阶段,板料接触凸模高点棱线A。但由于压边圈与上模未闭合,此时板料接触应力小,板料在A 点处不会留下硬化痕迹。第2 阶段,压边圈闭合,压边圈伴随模具下行,此时板料在凸模高点棱线A 处接触应力增大,硬化开始出现。第3 阶段,随着板料下行和材料的流动,在A点硬化的材料,会向高亮红点处流动。而B 处高点棱线,在此时也接触板料并伴随硬化发生。最后,在模具到底型面闭合时,就会出现图1 中A 与B 两处高点棱线,分别向外侧滑移,也就是在顶点发生的材料硬化,结束时到了红点的位置,即在红点处出现了滑移线缺陷。
滑移线解决方案
工艺设计上的解决办法
⑴调整冲压方向,使模具型面两侧均衡,减少滑移缺陷。如图4 所示,一个行李厢外板的工艺设计所示,在此零件最初的工艺设计时,冲压方向是沿车身方向旋转45°,进行模拟计算后,结果显示,在顶端棱线高点处,会发生沿箭头方向的滑移线缺陷。而后,在不断的试验模拟过程中,当我们将冲压方向调整为沿车身方向旋转30°时,模拟计算的结果实现,滑移线消除。

图4 所示工艺的断面,在模具刚刚闭合时,我们沿凸模顶点棱线到分模线这一距离,对模具型面和板料,分别计算断面线长度,会发现在将冲压方向调整到30°后,型面两侧的断面线差与板料在凸模顶点两侧的断面线差基本一致,如图5 所示。
考虑到板料在拉深过程中的流入,为避免滑移线发生,当我们在确定冲压方向时,应尽量使模具型面和板料在压边圈闭合时沿凸模顶点两侧断面平衡差值一致。

⑵调整工艺补充造型,延迟滑移时间。滑移线的发生是由于板料在凸模顶点的硬化,为避免滑移线发生,故当我们在确定冲压方向后,若能使棱线晚一些发生硬化,便能延缓滑移线的发生。
成形过程中板料在凸模棱线上滑过时,在最终产品上出现目视可见的二重线形状(可见带状曲线),此目视缺陷称为滑移线。
如图7 的断面图所示,翼子板车灯处也频发滑移线缺陷,在工艺设计时为避免滑移线的产生,在工艺补充白色圈的位置,设计了凸包的造型,目的是最大限度的延迟主棱线与板料发生接触硬化的时间,从而消除滑移缺陷。
⑶调整拉延筋及压边力,控制板料流动。有时,由于工艺设计的需要,当不可避免的存在型面断差时,为避免滑移线的发生,需要通过拉延筋控制板料的流动,来减缓滑移缺陷的程度。
如图8 所示,后背门零件的主棱线是零件中间的高点特征棱线,图示与顶盖搭接处是副棱线,如果工艺设计不做处理,此特征线会沿箭头方向滑移。在工艺设计调整冲压方向时,会以主棱线的成形情况作为调整依据,故不能通过调整冲压方向的手段来调整此处滑移,只能寻找其他手段消除。由图8 的断面图可见,此棱线位于凸模低点,本身接触板料硬化时间较晚,加上旁边有很多内板区域造型,故工艺补充对于此棱线滑移的减轻效果也有限。通过断面图可见,此工艺设计已经在背门的尾窗处设计了补充造型,用来控制板料流动,减缓滑移线缺陷,但效果应该仅占20%。此处流入量较大,工艺设计时,调整此处拉延筋的高度,通过控制流入量,结合补充造型的影响,可以有效减缓此处滑移线缺陷。

图9 调整副棱线大小减缓副棱线滑移
产品设计上的解决办法
⑴调整特征棱线的断面R 大小(15 ~20 倍料厚尺寸)。
当特征棱线所在的部位特殊,通过模具工艺无法解决时,应增加棱线R 的大小,根据棱线两侧型面的角度不同(产生的接触应力大小不同),按实际设计经验,棱线断面R 需要放大到零件料厚的15 ~20 倍。
图9 行李厢的主棱线由于造型需要,外侧出现拐弯,生产时虚线处会出现滑移,考虑到此处造型的影响,在将此局部圆角变更为20 倍料厚即R13 后,滑移缺陷消失。同样,图示机盖虚线处棱线,由于处于两侧,结合工艺设计和产品造型的要求,在将此圆角放大到15 倍料厚即R10 后,滑移缺陷消失。
⑵棱线R 无法增加时,需要满足的设计条件。当由于产品造型的需要,棱线圆角无法放大,而工艺设计又没有解决方案的售后,我们往往需要考虑与产品造型部门沟通,尝试调整周围造型,来解决现场的生产缺陷。
例如,圆角小而尖时,可尝试将圆角两侧型面的角度增加,或在发生滑移线的方向,在凸圆角下增加凹圆角来解决。由于现代车辆外观讲求独特化,造型都比较复杂,零件的设计方案也不可一味按照车企的产品造型标准进行设计(图10),必须通过模拟仿真进行验证,才能避免将制造问题带到生产现场。
车间现场的解决办法
有时,由于产品造型的局限性,或工艺设计的需要,滑移线必不可少的留到了生产车间,此时车间就只能在生产允许范围内尽可能减轻滑移线缺陷。但由于生产阶段应对此问题的手段确实有限,主要还是应该在产品造型和工艺设计阶段解决,下面给出3 种车间调整方法。
⑴移动缺陷位置。车间的调整只能基于可调参数进行,如机床参数,模具上的标准件等。一般可通过调整机床压力配合模具上板料定位件,来改变模具的压边力,改变材料的流动速度来消除滑移线缺陷。当零件本身存在内板区域时,也可控制材料流动,使滑移线滑动到内板区域,来达到掩盖缺陷的目的。
⑵减少接触冲击。滑移线的生成,最初的原点还是板料与凸模圆角发生接触硬化,所以减弱接触冲击,便可以最大化的减弱滑移线缺陷。而在车间现场能够调整的手段有以下3 条:①降低滑块速度,减小冲击速度,以此减缓冲击,但此方法会降低生产效率。②在不改变产品造型和保证检验合格的基础上,尽量将棱线圆角打磨均匀,减缓冲击尖点。但此方法由于需要手工打磨,所以存在改变产品造型特征的风险。③更换板材,提高材料的抗冲击能力,但同样会改变其他成形条件,也存在成形风险。
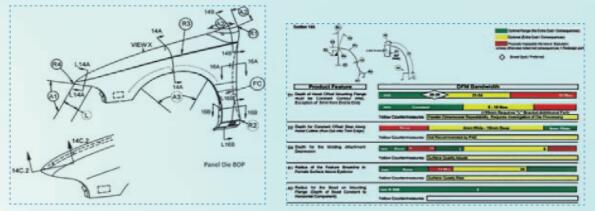
图10 翼子板产品造型标准
⑶返工打磨。有时,在一些特殊情况下,车间生产的零件不可避免地存在滑移线缺陷,此时就只能通过返工,由车间工人手工打磨的方式去除。
结束语
本文全面的研究了车身外板件滑移线的问题。介绍了滑移线的成因,并从冲压工艺设计、产品造型设计和车间现场调试三个方面提出了解决方法,可以为滑移线的消除提供现实可靠的参考价值。
张宇
冲压工艺工程师,主要从事冲压SE 分析、冲压项目管理、冲压现场管理、冲压工艺设计、冲压模具设计等,在14 年的工作中独立设计冲压模具120 余套,独立设计冲压工艺40 余套,SE 分析制件60 余套,积累大量的技术经验,并拥有1 项专利、2 篇论文。
滑移线是汽车外覆盖件在冲压生产中一种常见的表面缺陷,滑移线的出现严重影响了冲压件的表面质量和产品外观。本文主要对滑移线的产生原因和解决方案进行了详细的研究,为冲压设计和生产时避免滑移线的出现,提供了参考。