冲压工厂基于数字化的模具差异化预防性维护体系的建立(下)
文/严荣俊,杨成,陈文贵,杨帅军,沈镭·北京奔驰汽车有限公司
《冲压工厂基于数字化的模具差异化预防性维护体系的建立》(上)见《锻造与冲压》2020 年第22 期
实施推进
闭环控制管理
推动基于数字化的模具差异化预防性维护体系落地,闭环控制管理是核心。闭环控制就是将模具差异化预防性维护的理念利用“两维修、两维护、一改造”工作机制,通过数字化系统触发不同类别的工单,利用PDCA 闭环管理实现定期对各类工单的追踪、控制、案例总结、预防策略优化的过程管理。
在项目的实施与推进过程中,北京奔驰冲压工厂以模具差异化预防性维护理念为基础,按照时间周、月、年的层级分解指标任务,并对任务进行闭环控制管理与跟踪(图7)。
(1)根据年度任务指标以及上一年各生产线的运行状态量化、制定本年度工作目标。在年底召开总结会,分析总结全年工作内容和年度指标的完成情况。
(2)将年度工作目标细化分布于各个月份,制定单月工作目标,在月底召开例会总结本月指标完成情况,并根据完成情况制定或调整下个月的工作目标。
(3)将每个月份的工作目标细化分布于各周,各周工作内容围绕“差异化”理念,将具体的模具维修、维护工作以“两维修、两维护、一改造”的工作任务单形式展开。通过召开周例会总结一周以来的工作情况和工单任务跟踪情况,根据本周实际情况制定调整下周的工作目标或跟踪的问题。
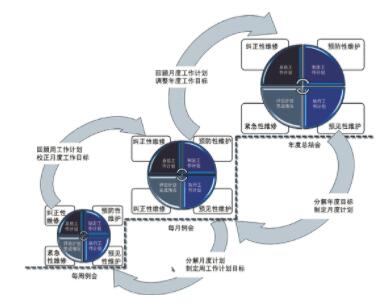
图7 闭环控制管理流程
在“差异化”的理念下,通过聚焦模具每天生产表现和出现的问题、梳理识别模具潜在的停机风险点,制定紧急和纠正性维修方案,通过大数据积累分析,优化制定其他同类模具的预见性和预防性维护策略。
健全班组工作机制
推动“模具差异化预防性维护”理念的落地,健全班组工作机制是基础。模修班组是模具维修、维护和改造的直接实施者,因此健全班组工作机制是项目实施与推进的基础。在“差异化”的理念指导下,北京奔驰冲压工厂模修工段从模具责任承包划分到个人、内部培训制度和Lesson Learned 经验总结反馈等方面做出改进。
(1)模具责任划分。
为了加快模修工对模具日常生产表现的熟悉程度和工作人员技能状态,每条生产线的模具按照难易程度依据2 ~4 人的小组划分责任承包(图8),这样每个小组成员都有经验丰富的老员工和技能还需要锻炼学习的青年员工,“一老带一新”的模式保证模具在线上生产和线下维修、维护都有负责人建立完善的模具档案,实时记录模具生产过程中出现的问题、制定对应的维修和维护策略。健全的模具维护信息记录便于工程师对故障进行统计分析,合理制定预见性和预防性维护计划。

图8 区域划分机制
在模具责任承包划分的基础上,引入考核激励机制,由班长对各小组担负模具的日常故障记录表、故障原因及预防性维护计划执行情况等进行抽查,检查结果纳入当年绩效。
通过在班组实施模具责任与承包的划分,优化了人员配置,加快了模具维修、维护的响应速度,相应的修正性维修计划也得到了保证。同时模具档案记录为模具的生产表现的判断提供了大量的数据基础,形成了预见性维护的依据。通过统计分析相关模具故障规律,预防性维护计划也得到了更好的修订与完善,整体工作效率得到了很大提高。
(2)内部培训制度。
针对日常模具故障、预防性维护和点检中发现的各种问题,冲压工厂模修工段建立了内部培训制度,以实战问题培养专家技能人才,以保障各项任务的顺利完成。在模具承包责任划分机制的基础上,总结模具常见故障和维修问题,整个同类模具发生的共性原因,确定内部培训内容。通过内部培训反馈结果,由班长或工程师判定是否需要形成单点课程,单点课程可作为现场工作手册指导班组工作。对于长期无法有效消除的故障,应建立持续性改进项目,根据项目难度确定项目负责人和参与人员,对模具进行改造从根源上杜绝故障的发生。由此反馈给新车型模具开发中加以设计优化。培训效果需要班长和工程师最终进行考核,根据最终考核结果修正培训流程,完善内部培训的评价机制。以2019 年MRA 冲压E 线为例,全年工作总结梳理各类单点课程及技术文件60 份,创新、改善项目5 份,全部形成现场指导手册,极大地提高了班组的整体维修能力。
(3)Lesson Learned 经验反馈。
模具停机故障的有些问题无法长期有效的消除,究其原因是在开发阶段,模具的工艺和结构设计存在局限和缺陷,通过定期的汇总形成文件,在日常培训总结同时,建立和模具开发设计部门生产规划PP 的月度模具经验Lesson Learn 反馈会,将实际发生的问题和一些经验建议,反馈传达至模具前期开发,在未来车型模具的设计和开发方面加以改进。
项目成果
本管理项目密切结合北京奔驰降本增效、精益管理的需求,系统地研究了序列化生产模具日常维修维护方面的管理能力问题,内容涉及模具差异化预防性维护管理工作思路及其推动落地方法研究,建立了与之配套的数字化系统,初步探索了智能维修,并成功在生产车间进行了示范应用验证。
(1)创新地提出了模具差异化预防性维护的工作理念。
基于精益管理的思想,北京奔驰冲压工厂创新地提出了模具差异化预防性维护的工作理念。通过维修、维护和改进三个环节的协调配合完成对设备的全方位管控,将维修人员从繁杂的被动维修工作中逐步解放出来,牢固树立了预防维修的理念,创建“修好故障模具是能力,维护好模具不出问题是本事”的团队文化,有力地保障了冲压精益生产和产品质量水平。
自项目2017 年启动至2019 年实施完毕以来,冲压工厂主力生产线生产停机率取得了明显下降(图9),A 线由2017 年的3.7%降低至2019 年的2%以下,伺服线E 线由2017 年的6%降低至2019 年的4%以下;伺服线由2018 年投产时的6.02%降低至2019 年的4.12%;降幅分别平均为46%,33.3%和32.1%;同时冲压件产品质量改善效果显著,零件质量不断提升,单车返修件数由2018 年的0.58 降至2020 年2 月的0.45;单车废品金额由2018 年的22元降至2020 年2 月的15 元(图10)。
(2)创建了一系列维修策略的推动落地方法。
在“两维修、两维护、一改进”工作理机制,引入闭环控制模型,通过逐级分解指标任务,周期性反馈工作成果为下个周期工作目标的制定提供依据,有效跟踪管理目标完成情况,通过管控全局使维护工作落地、时效、可控。
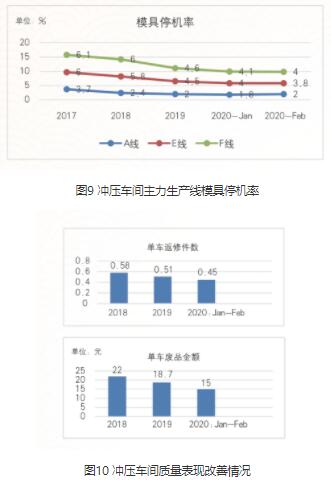
在班组管理方面,模具责任承包划分到个人、内部培训制度和Lesson Learned经验总结反馈等方面做出改进,加快维修反应速度,并对模具故障和运行状态进行记录跟踪从而形成预见性维护和预防性维护的制定依据;内部培训制度与人员能力等级评定制度的有效结合,能够很大程度上促进班组成员学习的积极性,有助于培养高水平维修保障人才,提高班组整体处理技能能力。
同时,通过大力鼓励技术人员持续消化吸收新技术以及建立创新改造项目,提升技术人员能力,为“两维修、两维护、一改造”的推动落地提供了强而有力的技术保障。
(3)建立了数字化的IT 模具维护管理系统。
根据模具差异化预防性维护的模型,建立了配套的IT 支持系统,实现了模具管理的数字化,具体包括工艺基础、模具停机数据采集与分析、模具备件管理、模具维护维修工单触发等核心模块,实现生产线冲次和模具、备件、数据分析于一体,各功能之间的数据互联,与模具工作的相关人员随时从系统中可以查看模具相关信息,实现数据的共享。
(4)实际经济价值评估。
据统计A 线平均停机成本1.3 万元/h,E 线平均停机成本3.5 万元/h,F 线平均停机成本4.6 万元/h;核算上周末和平时加班全年按照260 个工作日,每天10+10 工作模式。2018 年初至2019 年底共计500 个工作日,A 线计算节约成本500×10×2×1.7%×1.2=204万元;E 线停机节省成本500×10×2×2%×3.5=700万元;F 线停机节省成本(2018 年因投产不计算在内)260×10×2×2%×4.6=478.4 万元;合计2018 ~ 2019 年节省停机效益204+700+478.4=1382.4 万元。
质量节约方面,单车返修件数由2018 年的0.58降至2019 年底0.45;单车废品金额由2018 年的24元降至2019 年底15 元。冲压单件返修成本计算,2018 年和2019 年共计生产整车分别为48 万和56 万辆,故返修节约0.07×(480000+ 560000)×25=182万元;报废成本节约3.3×(480000 +560000)=343.2万元;合计质量方面每年大约节省升本101.5+ 191=292.5 万元,质量合计182+292.5=474.5 万元。
因此,通过基于数字化的模具差异化预防性维护体系建立项目的成功实施,2018 和2019 年北京奔驰冲压工厂在效率和质量两方面合计节省经济效益大约为1382.4+474.5=1856.9 万元。
《冲压工厂基于数字化的模具差异化预防性维护体系的建立》(上)见《锻造与冲压》2020 年第22 期